Maintenance coordination plays a vital part in guaranteeing the consistent operation and life span of different frameworks and resources. From mechanical apparatus to computer program applications, successful maintenance coordination.
Is basic to anticipate downtime, decrease costs, and maximize general proficiency. In this article, we’ll investigate the distinctive types of maintenance coordination and how they contribute to the smooth working of distinctive businesses.
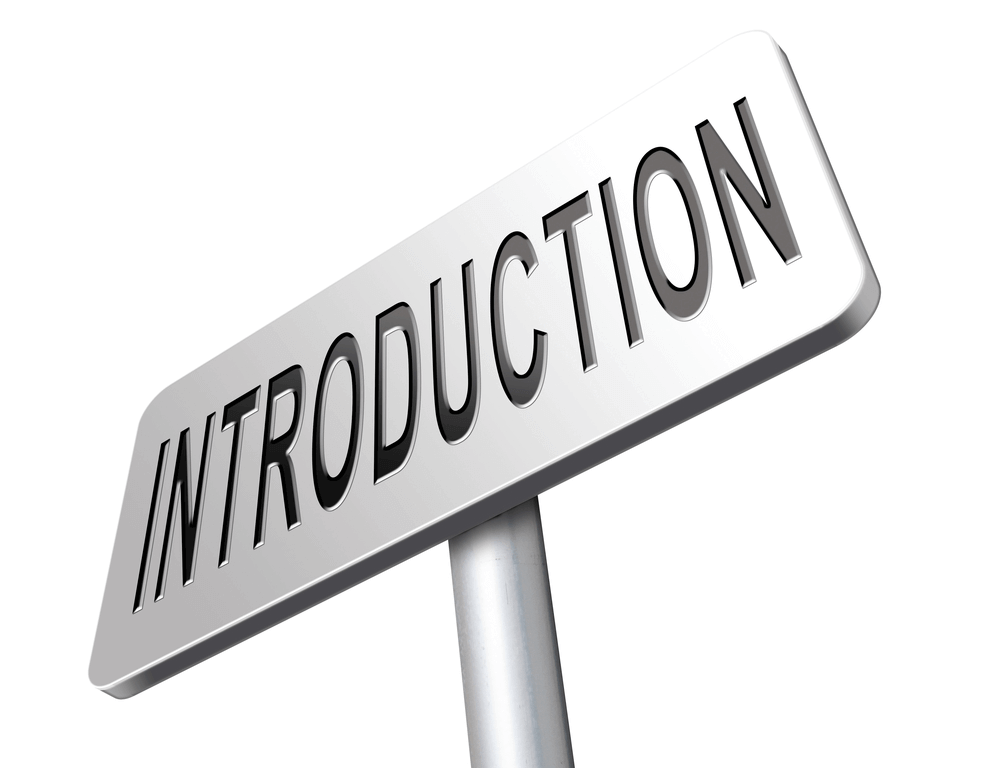
Maintenance coordination includes arranging, organizing, and overseeing the different exercises essential to keep gear, frameworks, and offices in ideal working condition. It envelops a run of procedures and approaches pointed at anticipating disappointments, tending to issues instantly, and amplifying the life of resources.
Types of Maintenance Coordination
- Preventive Maintenance: Preventive Maintenance Coordination may be a proactive approach that includes customary assessments, adjusting, and repairs to avoid potential issues from emerging. It takes after a foreordained plan and makes a difference in distinguishing and settling minor issues Sometimes they escalate into major breakdowns.
- Predictive Maintenance: Prescient maintenance depends on information and analytics to estimate when the hardware is likely to come up short. By utilizing sensors and advanced programs to monitor the condition of assets, maintenance can be conducted at the right time, reducing downtime and minimizing costs.
- Corrective Maintenance: Remedial maintenance is executed in response to identified issues or failures. It points to reestablishing the resource to its ordinary working condition as rapidly as possible, minimizing disturbances to operations.
- Planned Maintenance: Planned maintenance is planned in progress based on predefined criteria such as time, utilization, or condition. It guarantees that maintenance exercises don’t meddle with basic generation periods.
- Reactive Maintenance: Receptive maintenance is impromptu and happens in reaction to unforeseen disappointments. Whereas it can lead to downtime, its objective is to reestablish usefulness quickly.
- Condition-Based Maintenance: Condition-based maintenance includes checking the real-time condition of equipment and performing maintenance when particular conditions or edges are met. This approach optimizes maintenance endeavors and diminishes superfluous mediations.
Total Productive Maintenance (TPM)
TPM centers on maximizing hardware adequacy and worker association. It points to killing absconds, breakdowns, and mishaps while making strides in general effectiveness.
Reliability-Centered Maintenance (RCM)
RCM prioritizes support assignments based on their effect on the system’s unwavering quality. It points to discovering the foremost productive and cost-effective upkeep methodologies.
Risk-Based Maintenance (RBM)
RBM evaluates the dangers related to hardware disappointment and distributes assets in like manner. Basic resources get more consideration to play down potential results.
Scheduled Maintenance
Planned maintenance dispatching is scheduled at regular intervals, ensuring that equipment remains in excellent condition and operational.
- Unscheduled Maintenance: Unscheduled maintenance addresses startling disappointments and is frequently more expensive due to the criticalness included.
- Emergency Maintenance: Promptly performing crisis maintenance addresses critical issues that can cause security risks or significant production losses.
- Routine Maintenance: Schedule maintenance incorporates fundamental errands like cleaning, grease, and assessments that are significant for gear life span.
- Shutdown Maintenance: Answer Tenant shutdown maintenance happens amid hardware downtime and includes broad repairs and substitutions.
- Breakdown Maintenance: Following a complete failure, breakdown maintenance is carried out with the aim of restoring functionality as quickly as possible.
Importance of Maintenance Coordination
Compelling maintenance coordination guarantees that resources are accessible when required, decreases the chance of disappointments and amplifies the life expectancy of hardware. It upgrades efficiency, security, and cost-efficiency.
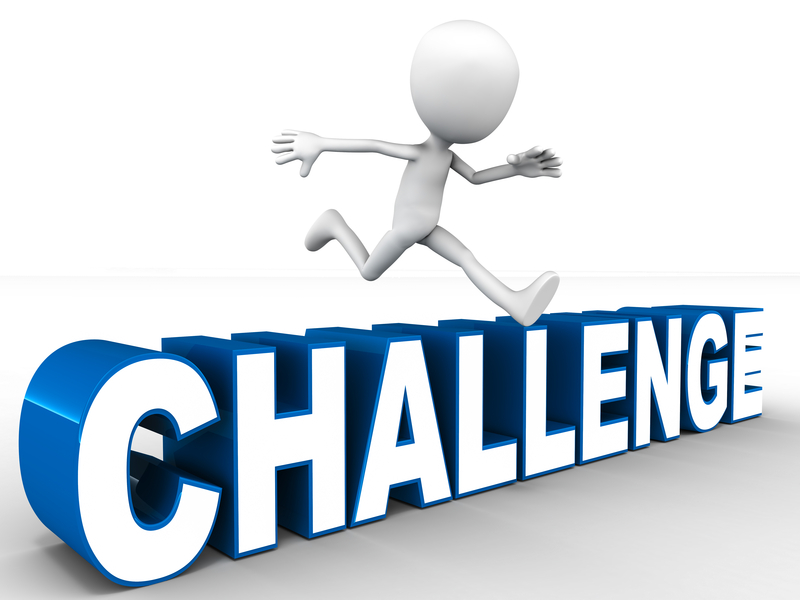
Executing maintenance coordination can be challenging due to asset limitations, complex planning, and the requirement for progressed advances. What is the Main Goal for Maintenance Coordination?
Benefits of Effective Maintenance Coordination
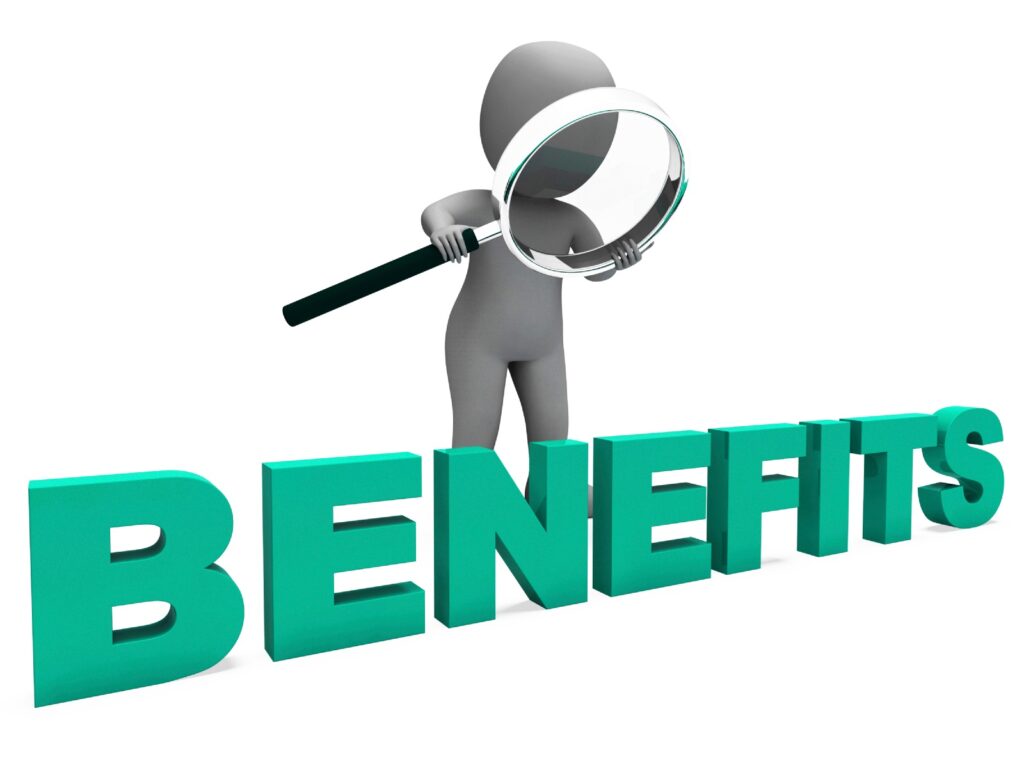
Effective maintenance coordination leads to expanded uptime, decreased maintenance costs, made strides in resource execution, and way better asset assignment.
Frequently Asked Questions (FAQ’s)
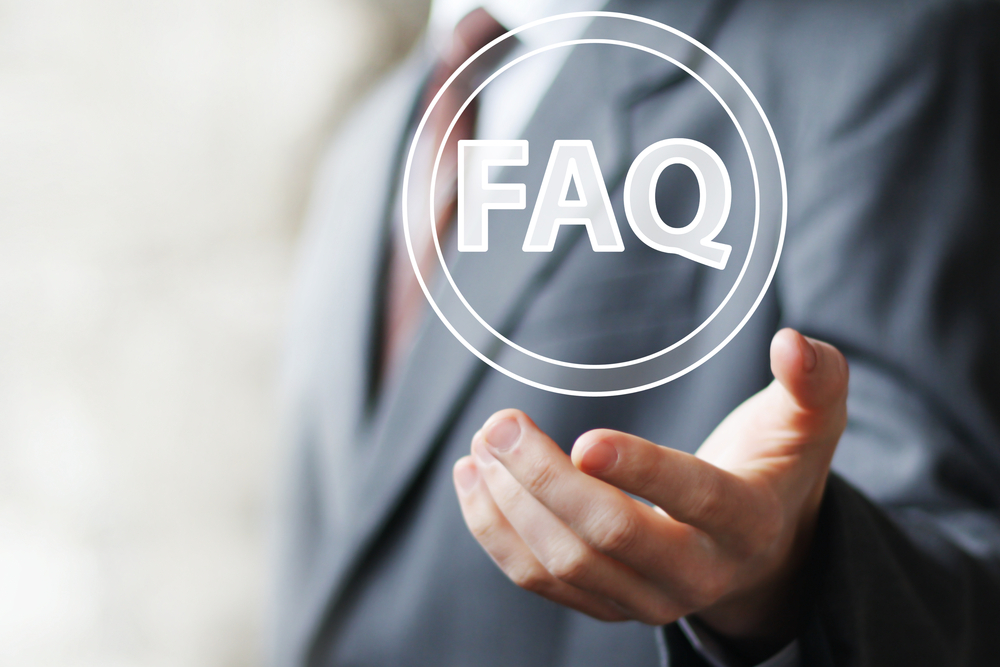
Preventive support includes planned assessments and repairs to anticipate hardware disappointments.
Prescient Maintenance Coordination employment information investigation to estimate gear disappointments, permitting convenient intercessions.
Crisis support points address basic issues quickly to avoid security risks and generation misfortunes.
Actualizing progressed innovations whereas overseeing complex plans can be challenging.
Add profitable maintenance points to improve proficiency, diminish abandons, and include workers in the maintenance preparation. You may also visit at Answer Tenant social media page for more informative information and interesting posts.
Conclusion
Maintenance coordination is the spine of solid and proficient operations in different businesses. By actualizing the correct maintenance techniques, organizations can minimize downtime, improve efficiency, and guarantee the longevity of their resources.